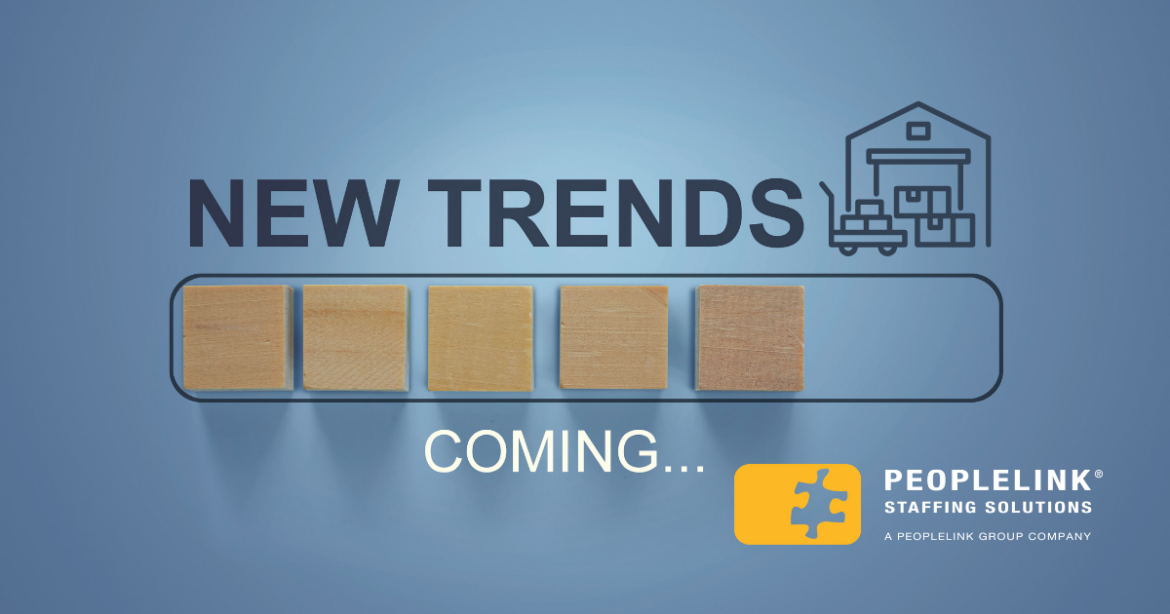
The shop floor is changing quickly. Technology, economic shifts, and evolving worker expectations are redefining how light industrial and manufacturing work gets done. From automation and reshoring to rising demand for workplace flexibility, job seekers are adapting to a fast-moving, opportunity-rich shift in how work gets done.
Let’s dive into the workface trends shaping the future of industrial employment—and what it means for your workforce strategy in 2025 and beyond.
Reshoring, Regional Growth, and the Road Ahead for U.S. Manufacturing
After years of offshoring, many companies have been bringing manufacturing operations back to the U.S.—a trend known as reshoring. Disruptions in global supply chains, rising overseas costs, and shifting geopolitical priorities have all accelerated the movement. According to the Reshoring Initiative, nearly 300,000 jobs were brought back to the U.S. in 2023, led by the automotive, electronics, and solar industries. However, recent changes to federal green energy and EV incentives could slow growth in some of these emerging sectors, potentially reshaping where future investments take root.
While not every reshoring effort results in immediate job growth, the broader shift toward domestic and regional production remains a powerful force—particularly in sectors supported by federal investment or sensitive to geopolitical risk. New and expanding facilities are increasingly located outside traditional metro hubs, particularly across the South and Midwest, opening new employment corridors.
What this means for job seekers:
- U.S.-based facilities are growing, especially in essential and tech-forward sectors.
- Employers need dependable local talent ready to grow with the company.
- New job opportunities are emerging in smaller cities and regional job hubs.
But it’s not just about where jobs are, it’s about how they’re done.
Automation Is Reshaping Job Requirements, But Not Replacing Workers
Automation continues to evolve, but people are still at the heart of the operation. Instead, it’s changing how work gets done. Robotics, AI, and smart systems now support tasks like quality control, inventory management, and packaging.
A McKinsey Global Institute report found that while about 50% of work activities could be automated using current technologies, fewer than 5% of occupations can be fully automated. However, about 60% of jobs involve tasks where at least one-third could be automated meaning significant changes are coming to how many people do their work.
The takeaway? Most jobs aren’t disappearing, but many are evolving. Adaptability and upskilling will be essential across nearly every role.
What matters now:
- Know your way around a tablet or dashboard? That’s a hiring edge.
- Quick learners and adaptable thinkers are rising fast, experience isn’t everything.
- Hands-on roles involving dexterity, decision-making, or judgment remain vital.
For job seekers: If you can troubleshoot a system or learn new tech on the fly, you’re already ahead. Many employers are offering on-the-job training to help workers upskill quickly.
And while tech changes how work gets done, flexibility is reshaping how teams are built.
Flexibility Is Now a Competitive Advantage
Most light industrial roles require physical presence but that doesn’t mean flexibility is off the table. Employers that build in flexibility are seeing faster fill rates and stronger retention, especially when they offer options like:
- Predictable schedules
- Compressed workweeks (e.g., 4-day shifts)
- Variable weekly hours
- Temp-to-hire opportunities
For employers: Staffing firms can help structure shift models that meet both business needs and worker preferences making flexibility a tool, not a trade-off.
The Skilled Labor Gap Isn’t Going Away
Despite wage increases and more open roles, the talent gap in manufacturing is still growing. A wave of retirements and lack of new entrants is making it harder to find qualified talent. The National Association of Manufacturers projects that the manufacturing sector is projected to face a shortfall of 2.1 million workers by 2030.
How staffing agencies help:
- We access broader candidate pools, including veterans and career changers.
- We screen for potential and trainability not just credentials.
- We help workers grow into skilled roles with coaching, client feedback, and reskilling paths.
ESG and Safety Culture Are Influencing Hiring and Retention
Environmental, Social, and Governance (ESG) priorities are showing up on the shop floor as sustainability and values become a regular part of the hiring conversation. Today’s workers are asking:
- Is this a safe and respectful workplace?
- Does the company care about its people and community?
- Are there opportunities to grow?
Manufacturers that prioritize DEI, safety, and environmental responsibility are seeing higher engagement and lower turnover especially among younger workers. These investments also strengthen employer brand, as today’s workforce increasingly seeks out companies whose values align with their own.
Workforce Compliance Is Under the Microscope
Increased scrutiny around employment verification and immigration is creating new pressures for manufacturers and other industrial employers. I-9 audits and even ICE raids have affected facilities that rely on large frontline workforces.
For employers:
- Make sure employment documents are current and stored properly.
- Conduct internal audits and use E-Verify to stay ahead.
- Partner with a staffing firm that understands compliance inside and out.
For job seekers: Expect to be asked for documentation more than once. Having up-to-date records ensures faster placement and avoids delays.
At Peoplelink, we follow strict compliance protocols and train our recruiters to stay current with legal requirements so both customers and candidates are protected.
Data Centers: A Growing—but Specialized—Sector
The rise of cloud computing, AI, and e-commerce has fueled the construction of new data centers. While many of the available roles are tied to data center construction, there are also ongoing operational positions for those with the right skill set.
In-demand roles include:
- Facilities maintenance
- HVAC and electrical technicians
- Equipment handlers and installers
However, these sites often run lean once built, and most long-term roles require specialized technical training. Still, for job seekers with the right skills, or those willing to train, data centers offer an exciting intersection of tech and industry.
The Bottom Line
Manufacturing and light industrial jobs are no longer defined by routine labor but by adaptability, tech integration, and long-term opportunity. The future of manufacturing belongs to those ready to adapt and we’re here to help you move forward.
Want to talk about how these trends affect your team or your career path? Let’s connect.